Understanding Plastic Injection Mold: A Key in Modern Manufacturing
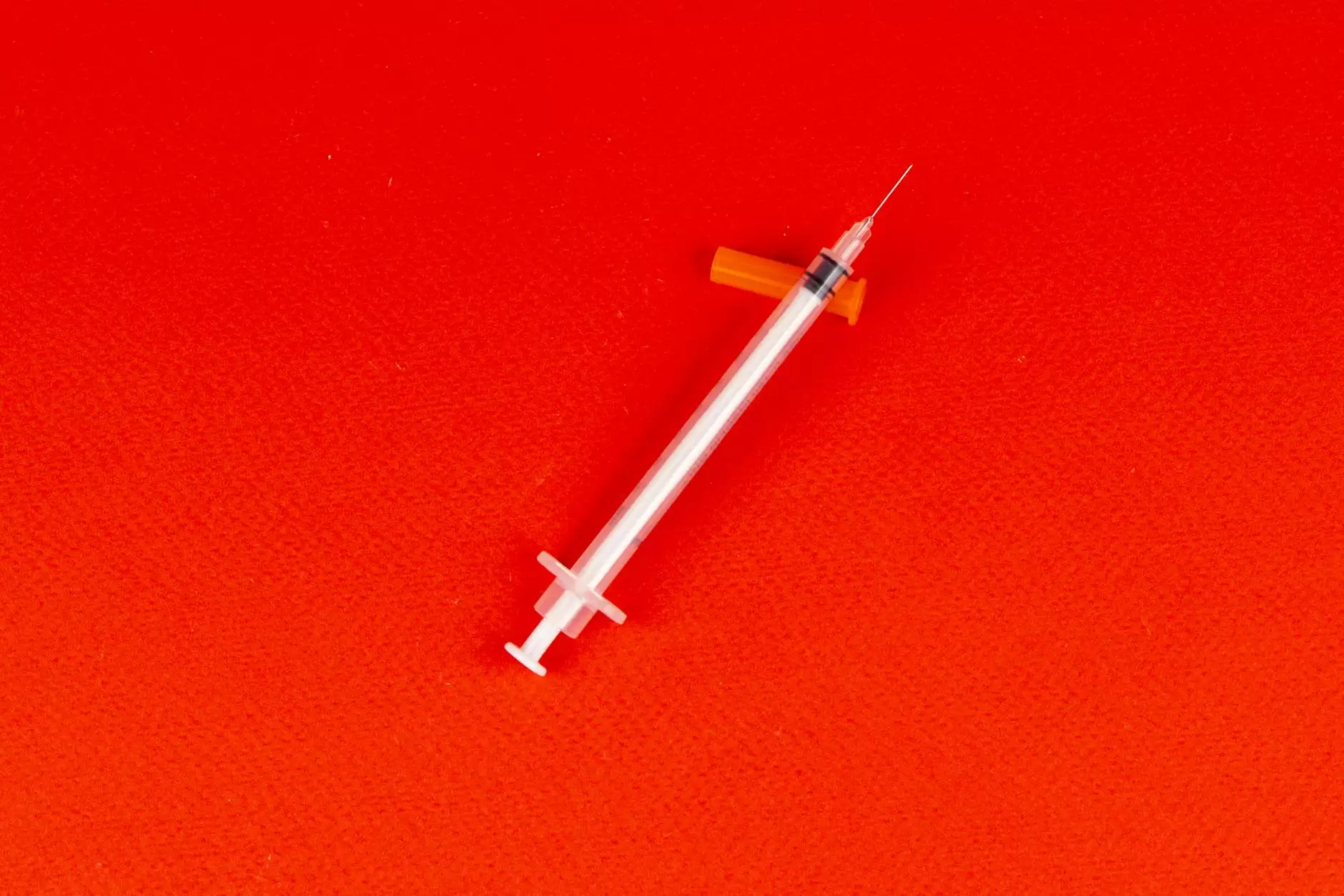
Plastic injection molding is a revolutionary process that has transformed the manufacturing landscape for countless industries. Whether it is household goods, automotive parts, or electronic components, the ability to create complex designs and high-volume products efficiently has been made possible through this advanced technology. In this comprehensive article, we will delve deep into the world of plastic injection molds, exploring their significance, processes, and the myriad applications they serve.
The Basics of Plastic Injection Molding
At its core, plastic injection molding is a manufacturing process for producing parts by injecting molten material into a mold. The process involves several key steps:
- Heating the Material: Plastic pellets are heated until they melt into a liquid state.
- Injection: The molten plastic is injected into a mold cavity under high pressure.
- Cooling: The material cools and solidifies in the shape of the mold.
- Demolding: Once cooled, the mold is opened, and the finished part is removed.
Types of Plastic Injection Molds
Understanding different types of molds used in this process is crucial for selecting the right approach for manufacturing requirements. Here are some common types:
- Single Cavity Mold: Used for producing a single part per cycle.
- Multicavity Mold: Designed to produce multiple identical parts in one cycle, enhancing efficiency.
- Family Mold: Able to produce different parts in one cycle, which can reduce costs significantly.
- Two-shot Molds: Allows the injection of two different materials, enabling the creation of composite parts.
- Insert Molds: Utilizes inserts like metal or other materials, which are integrated within the injection process.
The Advantages of Using Plastic Injection Molds
The advantages of plastic injection molds are numerous, making them a preferred choice in various manufacturing processes:
- High Efficiency: The ability to produce large volumes of parts at a rapid pace is unmatched.
- Precision and Quality: Injection molding produces consistent, high-quality parts with tight tolerances.
- Material Versatility: A wide range of materials can be used, including thermoplastics, elastomers, and thermosetting plastics.
- Low Waste: The process is highly efficient, producing minimal waste as the excess material can be reprocessed.
- Complex Geometries: Capable of creating intricate designs that would be difficult or impossible with other methods.
Plastic Injection Mold Applications
Industries worldwide utilize plastic injection molds for various applications. Here are a few sectors where this process plays a critical role:
1. Automotive Industry
The automotive sector heavily relies on injection molding for components such as dashboards, bumpers, and various internal parts. The durability and lightweight nature of molded plastics make them ideal for modern vehicles.
2. Consumer Electronics
From mobile phone casings to electronic housings, high-precision molded parts are essential for both functionality and aesthetics in electronics.
3. Medical Devices
The healthcare industry uses injection molding to create components for medical devices, such as syringes, surgical equipment, and drug delivery systems. These components must meet stringent regulatory standards, and injection molding allows for the production of reliable, sterile parts.
4. Packaging Solutions
Custom molded packaging provides a protective layer for products, ensuring safe delivery and enhancing branding through unique shapes and designs.
5. Household Items
From containers to furniture components, everyday products benefit immensely from the advantages of plastic injection molding, allowing for durable and affordable consumer goods.
Cost Considerations in Plastic Injection Molding
While plastic injection molding offers numerous advantages, businesses must carefully consider the cost aspects involved:
1. Initial Tooling Costs
The cost of creating the molds can be significant, especially for complex designs. However, this cost is distributed over large production runs, making it economical in the long run.
2. Material Costs
The choice of materials will greatly influence the overall expenditure. It is essential to select the right type of plastic that meets performance requirements without exceeding budget constraints.
3. Production Volume
The more units produced, the lower the cost per piece typically becomes. For small runs, other manufacturing processes may be more cost-effective.
4. Labor Costs
Automated injection molding machines can significantly reduce labor costs, which is a crucial aspect for high-volume manufacturers.
The Future of Plastic Injection Molding
As technology continues to evolve, so does the field of plastic injection molding. Innovations such as 3D printing are beginning to influence traditional methods, leading to new hybrid processes that increase customization options and reduce waste. Additionally, there is a growing emphasis on sustainability, with efforts to develop biodegradable plastics and recycling methods that can create a closed-loop manufacturing system.
Conclusion: Embracing the Power of Plastic Injection Molds
In conclusion, the world of plastic injection mold technology is vast and incredibly impactful across numerous industries. With the ability to produce high-quality, precise, and durable products, injection molding stands as a cornerstone of modern manufacturing. Businesses looking to enhance their production capabilities must consider integrating this technology into their processes. At DeepMould.net, we are committed to providing top-notch solutions and expertise in the field of metal fabrication and injection molding, driving forward the efficiency and quality that companies expect in today's competitive landscape.
Contact Us
If you are interested in how plastic injection molding can benefit your business, contact us at DeepMould.net to explore our services and solutions tailored for your needs.