Understanding Emergency Escape Breathing Apparatus (EEBA) for OSHA Compliance
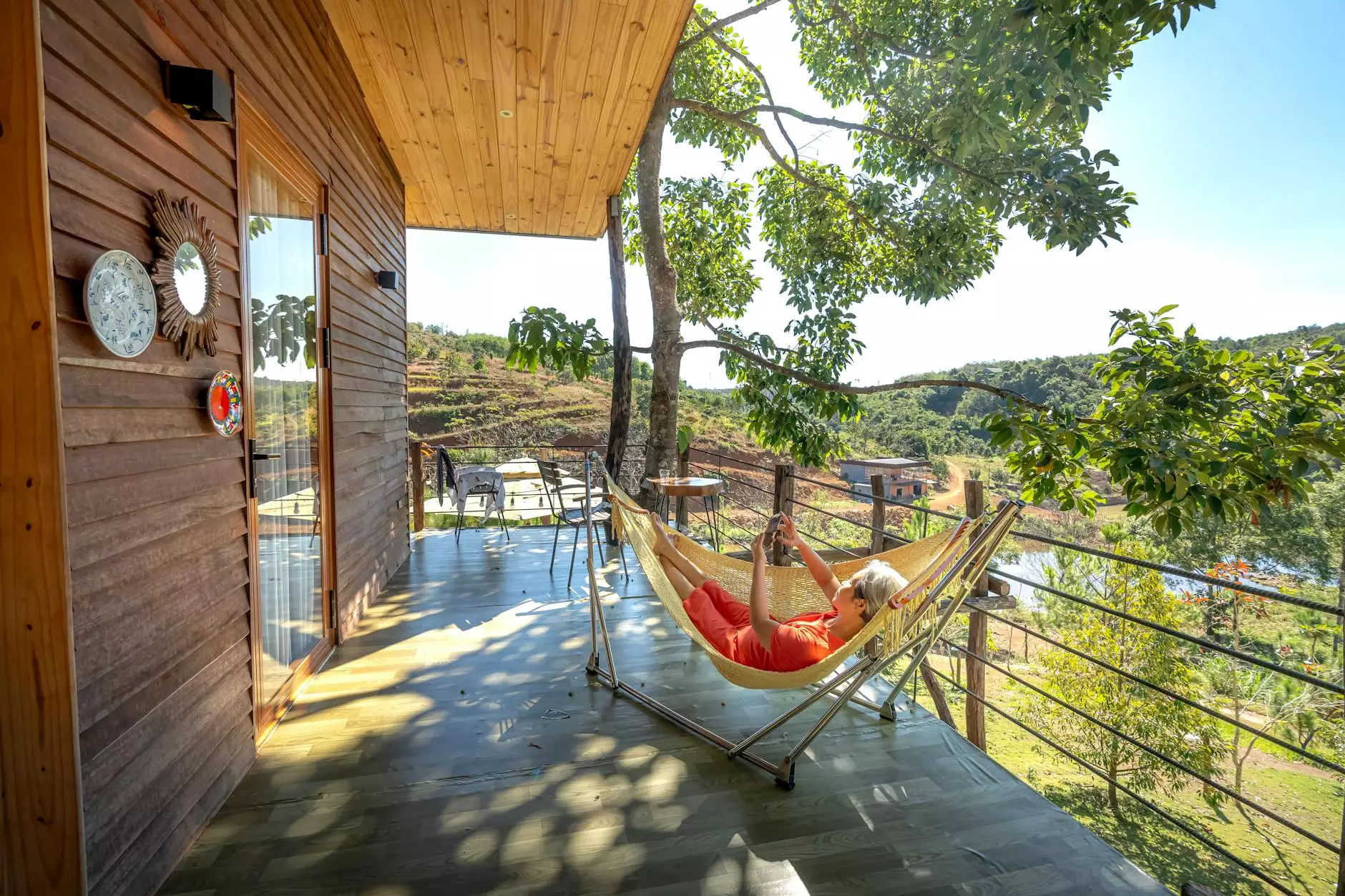
Emergency Escape Breathing Apparatus (EEBA) plays a critical role in ensuring workplace safety, especially in environments where hazardous materials are present. Under the guidelines set forth by The Occupational Safety and Health Administration (OSHA), it is essential for business owners and safety managers to comprehend the requirements and functionalities of EEBA systems. This article will delve into the intricate details of EEBA, its importance in maintaining safety standards, and how organizations can effectively implement these systems to ensure compliance with OSHA regulations.
What is Emergency Escape Breathing Apparatus (EEBA)?
Emergency Escape Breathing Apparatus (EEBA) refers to a type of respiratory protective equipment designed specifically for emergency situations. Typically employed in workplaces where air quality may become compromised due to toxic gases, smoke, or insufficient oxygen, the EEBA provides a safe means of escape for employees. Unlike other breathing apparatus options, the EEBA is lightweight, user-friendly, and intended solely for escape purposes, not for extended use in a hazardous environment.
The Significance of EEBA in OSHA Compliance
OSHA emphasizes the necessity of respiratory protection in the workplace, particularly in industries such as construction, manufacturing, and emergency response. The use of EEBA is crucial for compliance with OSHA regulations, which mandate that employers provide appropriate safety equipment and training to their personnel. Understanding the significance of EEBA will enhance safety measures and contribute to a positive safety culture within an organization.
Key OSHA Regulations Pertaining to EEBA
- 29 CFR 1910.134: This regulation outlines the respiratory protection program requirements, mandating that employers assess potential hazards and provide suitable respiratory protection, including EEBA where necessary.
- 29 CFR 1910.151(c): This section addresses the need for emergency response measures in workplaces involving hazardous substances, including the proper use of EEBA during emergencies.
- 29 CFR 1926.350: This regulation pertains to the requirements for gas welding and cutting, indicating the need for proper respiratory protection in environments with potential airborne contaminants.
Components of Emergency Escape Breathing Apparatus
Modern EEBA units comprise several essential components designed to ensure user safety and usability. Understanding these components is vital for effective use during emergencies.
1. Facepiece
The facepiece is the primary interface between the user and the breathing apparatus. It is designed to provide a secure seal around the face to prevent the ingress of harmful air. Facepieces can come in various forms, including:
- Full Face Masks: Covering the entire face, these masks also provide eye protection.
- Half Masks: Covering only the nose and mouth, these are lighter but do not provide eye protection.
2. Air Supply
EEBA typically utilizes compressed air or oxygen. The air supply must be sufficient to allow for a safe exit from hazardous areas. Common air supply configurations include:
- Compressed Air Cylinders: Portable and ready to use, they offer a limited duration of breathable air.
- Demand Valves: These automatically provide air when the user inhales, conserving air supply.
3. Harness System
The harness system secures the EEBA to the user and ensures comfortable wear in emergencies. Comfort is essential for immediate action during an emergency escape scenario.
Benefits of Implementing EEBA in the Workplace
The benefits of incorporating Emergency Escape Breathing Apparatus into your workplace safety protocols are substantial. These advantages not only enhance employee safety but also bolster organizational reputation and compliance.
1. Enhanced Safety Measures
By ensuring employees have access to EEBA, businesses dramatically improve their emergency response capabilities. Fast and efficient escape from hazardous situations can save lives.
2. OSHA Compliance
Integrating EEBA facilitates compliance with OSHA regulations. Being compliant not only avoids legal penalties but fosters a culture of safety and responsibility within the organization.
3. Employee Confidence
Employees are more likely to feel confident and secure in their workplace when they know that adequate safety measures, such as EEBA, are in place. This translates to increased productivity and morale.
4. Corporate Image
Companies that prioritize employee safety bolster their public image and can enhance customer trust and loyalty. This is especially critical in industries where safety risks are prevalent.
How to Implement an Effective EEBA Program
To maximize the benefits of EEBA, organizations must develop a comprehensive implementation plan. This involves selecting the right equipment, training employees, and establishing regular maintenance protocols.
1. Assess Workplace Hazards
The first step in implementing an EEBA program is conducting a thorough assessment of workplace hazards. This entails identifying potential scenarios where an EEBA would be necessary. Consider factors such as:
- The presence of hazardous chemicals.
- Likelihood of fire or smoke.
- Work processes that may produce toxic gases.
2. Selecting the Correct EEBA Type
Based on the hazard assessment, select the appropriate type of EEBA. Consulting with safety professionals and reviewing OSHA guidelines will aid this decision. Consider factors such as:
- Duration of air supply required.
- Environmental conditions (temperature, humidity).
- Comfort fit for varied employee demographics.
3. Training Employees on EEBA Use
Providing comprehensive training on the proper use of EEBA is crucial. Training should cover:
- Proper donning and doffing procedures.
- Recognizing when to use the apparatus.
- Conducting routine inspections and maintenance.
4. Regular Maintenance and Inspection
Regular maintenance is essential for ensuring that EEBA remains functional and effective. Establish a schedule for:
- Routine checks on the air supply levels.
- Inspection of masks and other components for wear and tear.
- Replenishment of supplies as necessary.
Conclusion
Incorporating Emergency Escape Breathing Apparatus (EEBA) is a fundamental component of workplace safety, particularly in industries subject to OSHA regulations. Understanding the functionalities, benefits, and implementation strategies for EEBA can empower organizations to create a safer work environment. Investing in EEBA not only fulfills legal obligations but also demonstrates a commitment to employee safety and well-being.
As organizations move forward, it is crucial to remain vigilant about updates to OSHA regulations and advancements in safety technology to ensure that your workforce is protected both today and in the future. By prioritizing the integration of Emergency Escape Breathing Apparatus into your safety strategy, you are not just complying with regulations; you are actively safeguarding the lives of your employees and fostering a sustainable business model.
emergency escape breathing apparatus osha