Understanding Custom Injection Molding Companies: Revolutionizing Manufacturing
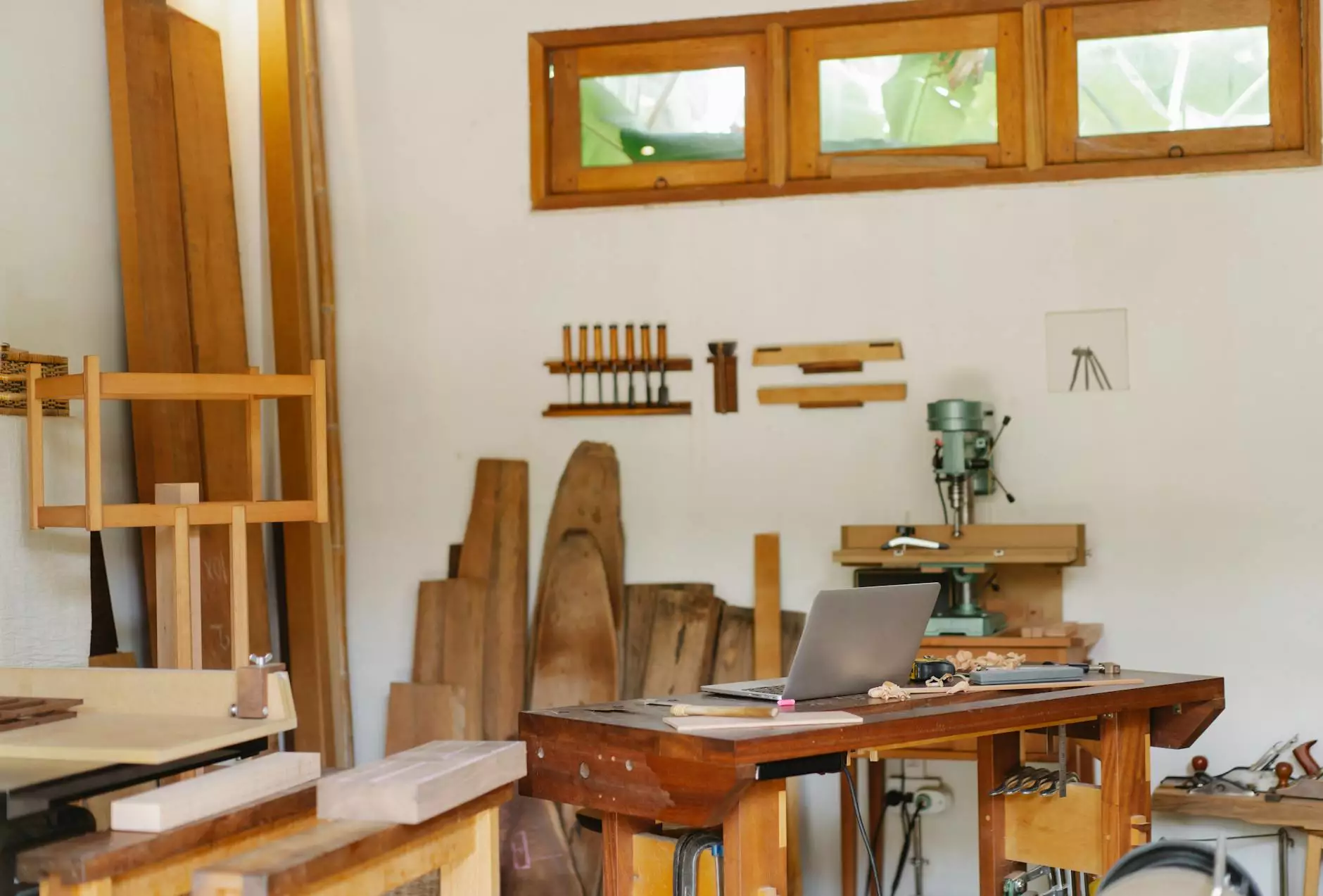
Custom injection molding companies play a pivotal role in modern manufacturing, transforming plastic materials into intricate and precise components. This process not only enhances productivity but also significantly reduces waste, offering an eco-friendly alternative in product development. In this comprehensive article, we will explore the intricacies of injection molding, the benefits of partnering with these companies, and their impact on various industries.
The Process of Custom Injection Molding
Injection molding is a manufacturing technique that involves injecting molten material into a mold to create specific shapes and designs. The process typically includes the following steps:
- Material Selection: The first step is selecting the appropriate thermoplastic or thermoset material. Common choices include ABS, polycarbonate, and nylon.
- Mold Creation: A mold designed to the client’s specifications is manufactured, often using CNC machining or 3D printing.
- Injection Process: The chosen material is heated until molten and injected into the mold under high pressure.
- Cooling: The injected material cools and solidifies, adopting the mold's shape.
- Finishing: The molded part is ejected, and any finishing processes, such as trimming or painting, can be applied.
Why Choose Custom Injection Molding Companies?
Partnering with custom injection molding companies brings a multitude of advantages. Here are the key benefits:
- Cost-Effectiveness: The high-volume production capability of injection molding significantly reduces the cost per unit, making it ideal for large-scale projects.
- Precision and Consistency: Injection molding allows for high precision in manufacturing, ensuring that each part is consistent and meets the required specifications.
- Design Versatility: With advanced technologies, these companies can create complex designs that might be impossible with other manufacturing methods.
- Reduced Waste: The injection molding process minimizes material waste by efficiently using the raw materials required for production.
- Scalability: As businesses grow, custom injection molding companies can adjust production levels to meet increasing demands.
Industries Benefiting from Custom Injection Molding
Custom injection molding has extensive applications across various sectors, including:
1. Automotive Industry
The automotive industry relies heavily on injection molding for creating numerous components, from interior dashboards to external casing. The precision and durability of molded parts contribute to overall vehicle performance and safety.
2. Medical Devices
Custom molded parts are critical in the medical field, where they are used to manufacture equipment like syringes, surgical instruments, and diagnostic devices. The ability to produce sterile, precise parts is especially important in this sector.
3. Consumer Goods
Everyday consumer goods, including kitchenware, toys, and electronic housings, frequently utilize injection molding for efficient mass production. This method ensures uniformity and functionality in design.
4. Aerospace
In aerospace manufacturing, injection-molded parts are valued for their lightweight and durable characteristics. These components contribute significantly to fuel efficiency and overall aircraft performance.
Choosing the Right Custom Injection Molding Company
When selecting a custom injection molding company, consider the following factors:
- Experience: Look for companies with a proven track record in your industry.
- Technology: Ensure that the company utilizes modern technologies and equipment to enhance productivity and quality.
- Quality Control: A robust quality assurance program is essential to maintain the integrity of the products.
- Customization Options: The ability to provide tailored solutions based on your specifications is critical.
- Customer Support: Strong communication and support throughout the process are vital for a successful partnership.
Future of Custom Injection Molding
The landscape of custom injection molding is continually evolving thanks to advancements in technology and production techniques. Some trends shaping the future include:
1. Sustainable Practices
With increasing environmental concerns, many custom injection molding companies are adopting sustainable practices, such as using recycled materials and reducing energy consumption during production.
2. Enhanced Design Capabilities
Innovations in computer-aided design (CAD) and additive manufacturing are expanding the possibilities for more complex and creative product designs.
3. Automation and Industry 4.0
The integration of automation and smart manufacturing technologies is streamlining processes, reducing labor costs, and improving overall efficiency in production.
Conclusion: A Valuable Partnership
In conclusion, custom injection molding companies are essential partners in today’s manufacturing landscape. Their ability to provide precision, efficiency, and customization makes them invaluable across a wide range of industries. By understanding the process, the benefits, and how to choose the right partner, businesses can leverage the full potential of injection molding to enhance their production capabilities and maintain a competitive edge in their respective markets.
For more information about the benefits of custom injection molding and to explore partnerships, visit us at Deep Mould.