Mastering Precision Plastic Molding for the Future of Manufacturing
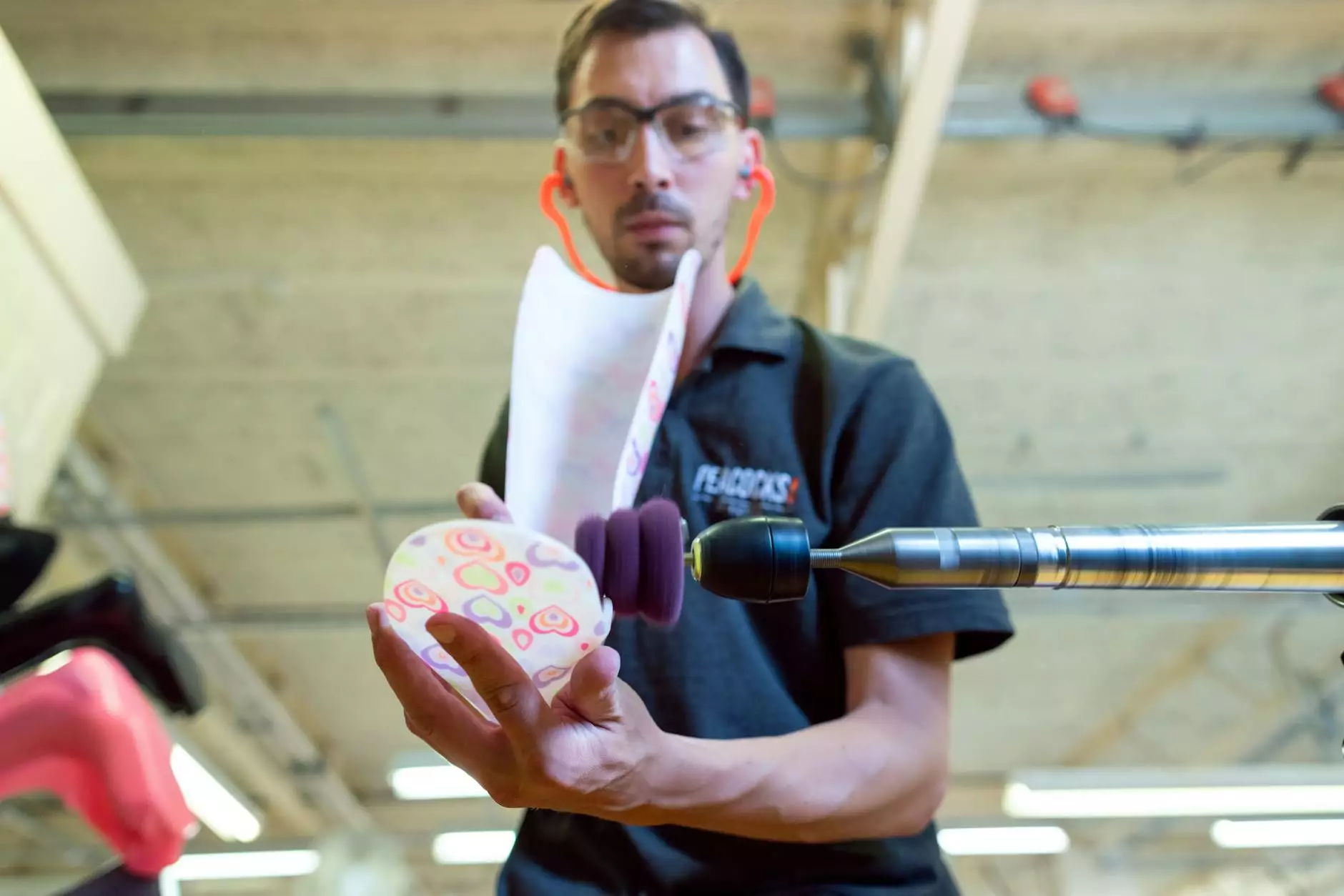
The realm of manufacturing has evolved remarkably over the decades, with precision plastic molding standing at the forefront as a preferred technique for producing complex and highly accurate parts. This article delves into its importance, advantages, and applications that make it indispensable in various industries.
What is Precision Plastic Molding?
Precision plastic molding is a manufacturing process where plastic is melted and injected into a precisely-crafted mold to create intricate components. This technique is favored for its ability to produce high volumes of parts with consistent quality and dimensional accuracy. The process typically involves:
- Material Selection: Choosing the right type of plastic, such as ABS, PVC, or polycarbonate, which affects the final product's strength and durability.
- Mold Design: Designing the mold is critical; it must reflect the exact specifications of the desired part.
- Injection Process: The plastic is heated to its melting point and injected into the mold under high pressure.
- Cooling and Ejection: After sufficient cooling, the mold is opened, and the finished part is ejected.
Advantages of Precision Plastic Molding
Businesses that adopt precision plastic molding reap numerous benefits. Understanding these advantages can help manufacturers optimize their production processes and enhance product development:
1. High Dimensional Accuracy
One of the most significant advantages of precision plastic molding is the exceptional dimensional accuracy it offers. This precision enables manufacturers to produce parts that meet stringent tolerance specifications, essential for sectors like automotive and medical devices where even minor deviations can result in costly failures.
2. Cost-Effectiveness
Over time, the precision plastic molding process is often more economical than traditional manufacturing methods, especially in high-volume production. The initial investment in high-quality molds may be substantial, but the per-part cost decreases significantly as production scales up.
3. Complex Geometries
Precision plastic molding allows for the creation of intricate designs that would be challenging to achieve with additive manufacturing or machining. This capability opens up opportunities for innovative product designs that can enhance functionality and aesthetics.
4. Material Versatility
With hundreds of different types of plastics available, manufacturers using precision plastic molding can select materials that cater to specific performance criteria, such as heat resistance, flexibility, or chemical stability. This versatility is invaluable across various industry applications.
5. Reduced Waste
The precision inherent in this molding process results in little excess material when producing parts. Waste reduction not only contributes to lower costs but also aligns manufacturing with sustainable practices, an increasingly important consideration for businesses today.
Key Applications of Precision Plastic Molding
The applications of precision plastic molding are far-reaching and can be found across a multitude of industries:
1. Automotive Industry
The automotive sector heavily relies on precision plastic molding to produce components such as dashboards, gear knobs, and various electronic housings. The demand for lightweight, fuel-efficient vehicles drives the need for high-quality plastic parts, which contribute to weight savings and performance improvements.
2. Medical Devices
In the medical field, stringent regulatory standards necessitate that devices are produced with superior precision. Components such as syringes, surgical instruments, and diagnostic equipment all benefit from the accuracy provided by precision plastic molding.
3. Consumer Electronics
From smartphone casings to computer components, the consumer electronics industry is another significant user of precision plastic molding. The need for compact designs that can withstand multiple uses and variations in temperature makes this molding technique the ideal choice.
4. Industrial Applications
Various industrial components, such as housings for motors, tools, and fixtures, leverage precision plastic molding for its durability and cost efficiency. Industries continue to adopt these solutions to optimize performance and reduce operational downtime.
Choosing the Right Partner for Precision Plastic Molding
When sourcing precision plastic molding services, partnering with the right company can make all the difference in the success of your project. Here are several criteria to consider:
1. Experience and Expertise
Look for manufacturers that have a solid track record in the industry. Experience often equates to a deeper understanding of materials, design complexities, and process optimizations, providing you with superior outcomes.
2. Technology and Equipment
Advanced machinery and the latest technology are crucial in achieving the precision required in molding processes. Ensure that your chosen partner invests in modern equipment and employs cutting-edge techniques.
3. Quality Assurance
Verify that the manufacturer adheres to strict quality assurance protocols. Certifications such as ISO 9001 can indicate a commitment to maintaining high-quality standards across production.
4. Customization Capabilities
Each project comes with unique requirements. A capable partner should demonstrate flexibility and the ability to customize molding processes to fit your specific needs, ensuring the best possible outcome for your products.
The Future of Precision Plastic Molding
As industries evolve, so does the field of precision plastic molding. Several trends indicate the future direction of this manufacturing process:
1. Sustainable Practices
With increased awareness of environmental issues, sustainable manufacturing practices are becoming vital. The development of bioplastics, which are more environmentally friendly, is likely to enhance the sustainability of precision plastic molding.
2. Automation and Smart Manufacturing
The integration of automation and smart technologies into molding processes will enhance efficiency, reduce human error, and improve production timelines. Expect greater use of AI-driven systems for quality control and predictive maintenance.
3. Advancements in Materials
Research into new materials will continue to push the boundaries of what is possible with precision plastic molding. Improved material properties will lead to even more applications in high-performance and specialized sectors.
Conclusion
In conclusion, precision plastic molding is a critical manufacturing process that not only enhances product quality but also enables innovation across various industries. By understanding its advantages and applications, as well as choosing the right partners, businesses can significantly benefit from this technology in their product development initiatives.